Zirconia ceramic shafts
E-mail:sales01@hkceramic.com
Zirconia ceramic shafts, also referred to as zirconia ceramic rods, harness the exceptional properties of zirconia (ZrO2), offering versatile solutions for industrial applications:
Exceptional Mechanical Properties and Wear Resistance
Zirconia boasts a Vickers hardness of 1175 GPa and an elastic modulus of 200 GPa, offering outstanding fracture resistance and wear resistance, making it ideal for use in heavy load environments.
Chemical Stability
The chemical inertness of zirconia ensures excellent performance in chemically aggressive environments, resisting a variety of corrosive chemicals.
High Fracture Toughness
With a fracture toughness of 9 MPa·m1/2, zirconia shafts are resistant to breakage under impact or high pressure.
Smooth Surface and Precision Manufacturing
The smooth surface of zirconia shafts helps reduce friction and wear, enhancing the efficiency and lifespan of moving parts.
Thermal Stability
With a thermal conductivity of 2.5 W/(m·K) and high thermal shock resistance (△T of 250°C), zirconia is suitable for environments with significant temperature fluctuations.
Zirconia ceramic shafts find extensive applications in multiple high-demand technical fields:
Chemical Processing Equipment
Used in pumps, valves, and other fluid control systems, where its corrosion resistance and wear resistance are crucial in handling corrosive chemicals.
Precision Machinery and Electronics
Employed as high-performance components in advanced printing equipment and precision instruments, zirconia ensures equipment operates with precision due to its wear resistance and stability.
Medical Devices
Extensively used in dental and orthopedic implants due to its biocompatibility and wear resistance, suitable for fabricating artificial joints and other implants.
Automotive and Aerospace
Utilized in high-performance engines and aerospace components, zirconia's high temperature resistance and mechanical stability provide additional safety assurance.
Zirconia ceramic shafts, renowned for their exceptional mechanical strength, wear resistance, chemical stability, and thermal stability, serve as critical components across various industries. They not only enhance equipment efficiency and lifespan but also deliver outstanding performance under high loads and extreme conditions. These characteristics make zirconia ceramic shafts indispensable in modern industrial applications, particularly in environments demanding superior material performance. Through precise design and manufacturing, zirconia ceramic shafts ensure high efficiency and long-term stability of application systems, meeting the ongoing demand for high-performance materials in the industry.
In the field of customized precision ceramic processing, our company specializes in producing a variety of high-performance ceramic components, including zirconia ceramics, silicon nitride, aluminum nitride, and more. These ceramic components exhibit excellent thermal stability, electrical insulation, high temperature resistance, and wear resistance, widely applied in critical sectors such as aerospace, electronics, machinery, defense, and automotive industries. With their exceptional performance and reliability, our products provide crucial support and assurance, helping customers enhance production efficiency and optimize product performance.
Dongguan Haikun New Material Co., Ltd.
A global advanced precision ceramics (special ceramics) manufacturer, focusing on the development, design, production and sales of advanced precision ceramic products, covering zirconium oxide, aluminum oxide, silicon nitride and other materials, which are widely used in aviation, aerospace, military industry, medical and other fields
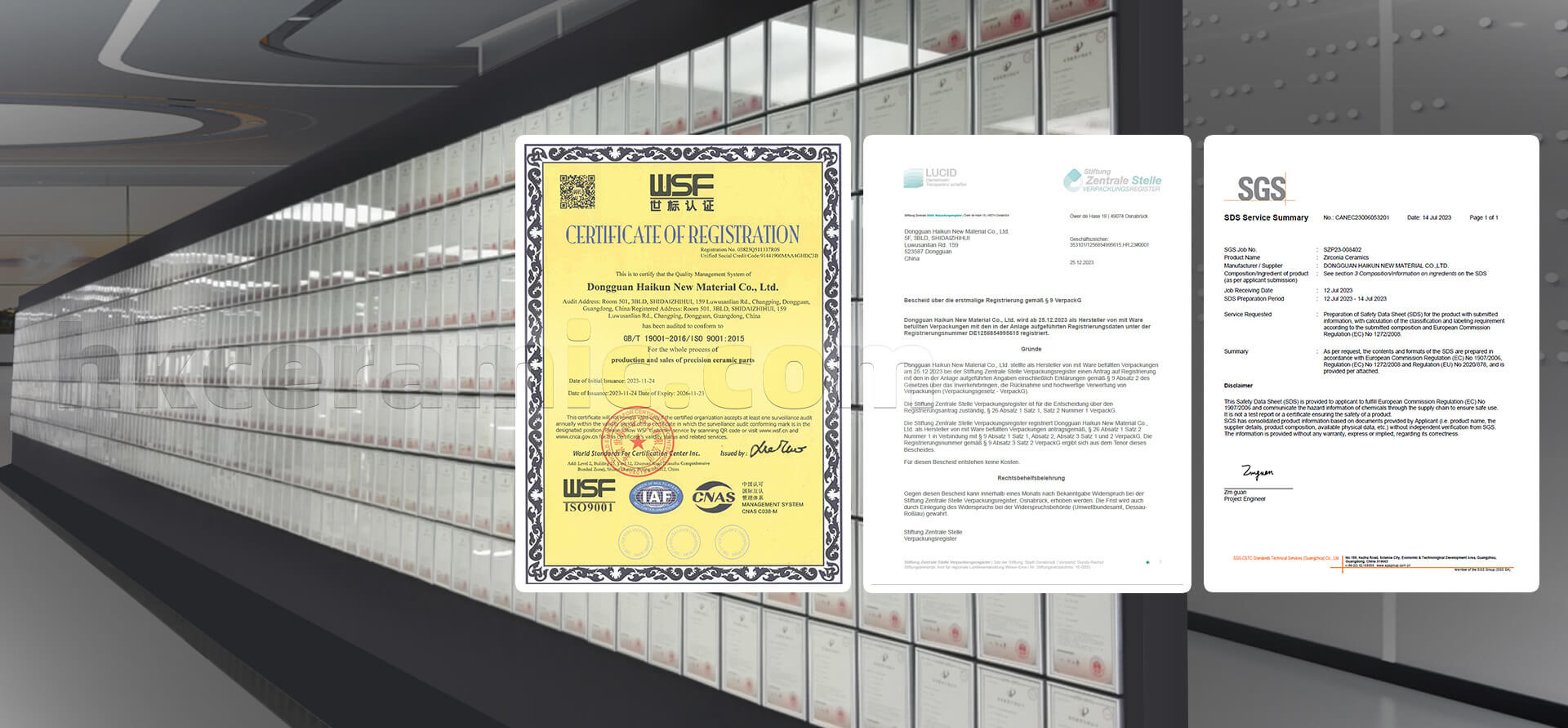
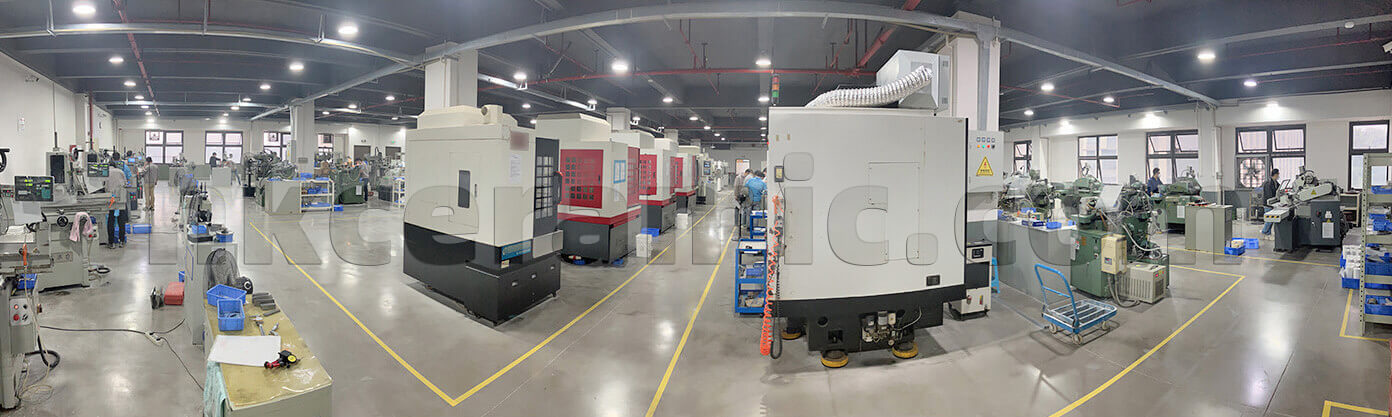
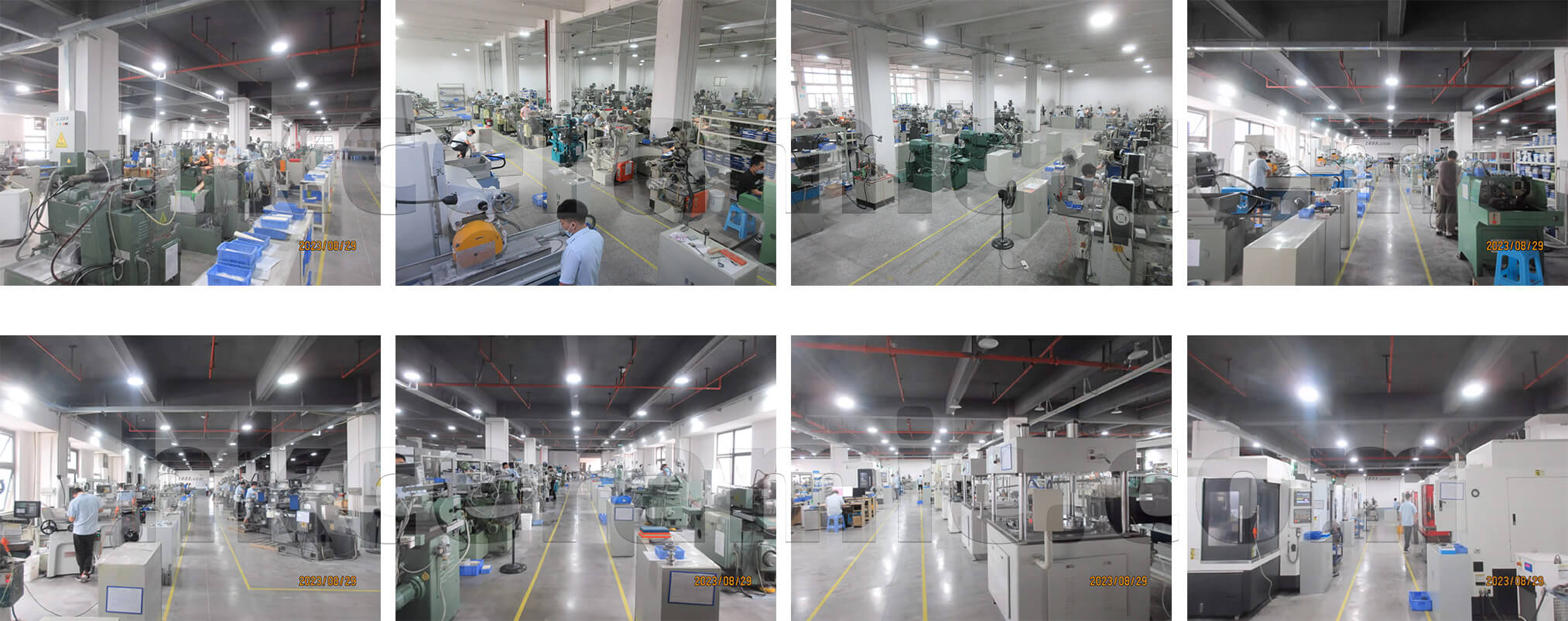
Comparison of ceramic material properties
Use our interactive ceramic material comparison chart to compare ceramic materials across different material properties.
Click the Property Button above to view the corresponding property comparison of precision ceramic materials
*The values in the table are typical material properties
Precision ceramic product customization process
Step 1
Contact us
Step 2
Technology Assessment
Step 3
Confirm the quotation
Step 4
Signing the contract
Step 5
Inspection and delivery
Step 6
Confirm Receipt