Alumina Ceramic Wheel
E-mail:sales01@hkceramic.com
Alumina ceramic wheel, also known as a porous ceramic sealing flange ring, demonstrates the outstanding physical and chemical properties of alumina (Al2O3):
High Hardness and Excellent Wear Resistance
With a Vickers hardness of up to 15.7 GPa, alumina ensures durability and long life in high-wear environments.
Good Thermal Stability
A thermal conductivity of up to 27.5 W/(m·K) combined with a maximum operating temperature of 1650°C allows it to maintain structural and functional stability in high-temperature applications.
Excellent Electrical Insulation
With a breakdown strength of up to >10 KV/mm and low dielectric loss, it is suitable for use as an insulating material in electrical applications.
Precise Perforation and Shape Design
The design includes multiple holes not only for fastening but also as channels for fluids or gases, enhancing its functionality in sealing and fluid control systems.
Smooth Surface Finish
A uniform white appearance and smooth surface help reduce friction, provide consistent sealing performance, and minimize leakage.
Alumina ceramic wheels have a wide range of applications in various industrial fields:
Chemical Processing
Used as sealing and isolation components in piping systems within high-temperature or corrosive environments, ensuring long-term reliability due to its chemical stability and heat resistance.
Precision Machinery and Electronic Devices
Employed in equipment that requires precise control of fluid flow and environmental stability, such as in semiconductor manufacturing and specialized machinery.
Medical Equipment
Suitable for various components in medical devices due to its biocompatibility and chemical resistance, especially in environments requiring strict sterile conditions.
Automotive and Aerospace Industries
Used in engine components and aerospace parts to withstand high temperatures and chemical corrosion, providing sealing and structural support.
Alumina ceramic wheels play a crucial role in modern industrial systems due to their excellent wear resistance, high-temperature stability, and electrical insulation properties. These characteristics make them ideal for high-temperature, high-corrosion, and high-wear conditions, particularly in fields like chemical processing, precision machinery, and medical equipment. The precise perforation and optimized shape design enhance structural integrity and improve performance efficiency during assembly and use. The versatility and high performance of alumina ceramic wheels ensure reliable long-term operation in challenging applications, meeting the ongoing demand for high-performance materials in the industry.
In the field of precision ceramic processing and customization, our company is dedicated to producing various high-performance ceramic components, including zirconia ceramics, silicon nitride ceramics, aluminum nitride ceramics, and more. These ceramic components exhibit exceptional thermal stability, electrical insulation, high-temperature resistance, and wear resistance, and are widely applied across critical sectors such as aerospace, electronics, machinery, defense, and automotive industries. Our products are known for their superior performance and reliability, providing essential support and assurance to our customers, helping them enhance production efficiency and optimize product performance.
Dongguan Haikun New Material Co., Ltd.
A global advanced precision ceramics (special ceramics) manufacturer, focusing on the development, design, production and sales of advanced precision ceramic products, covering zirconium oxide, aluminum oxide, silicon nitride and other materials, which are widely used in aviation, aerospace, military industry, medical and other fields
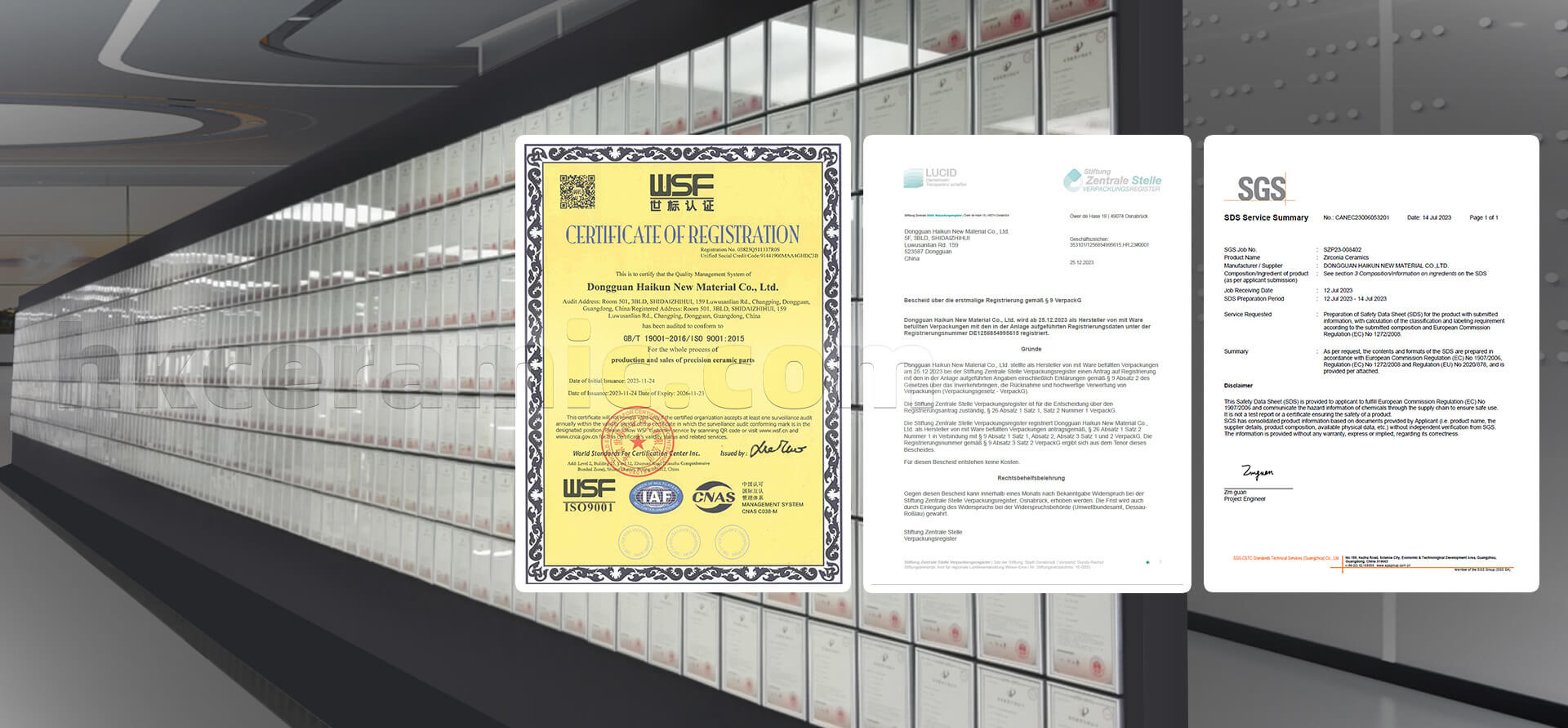
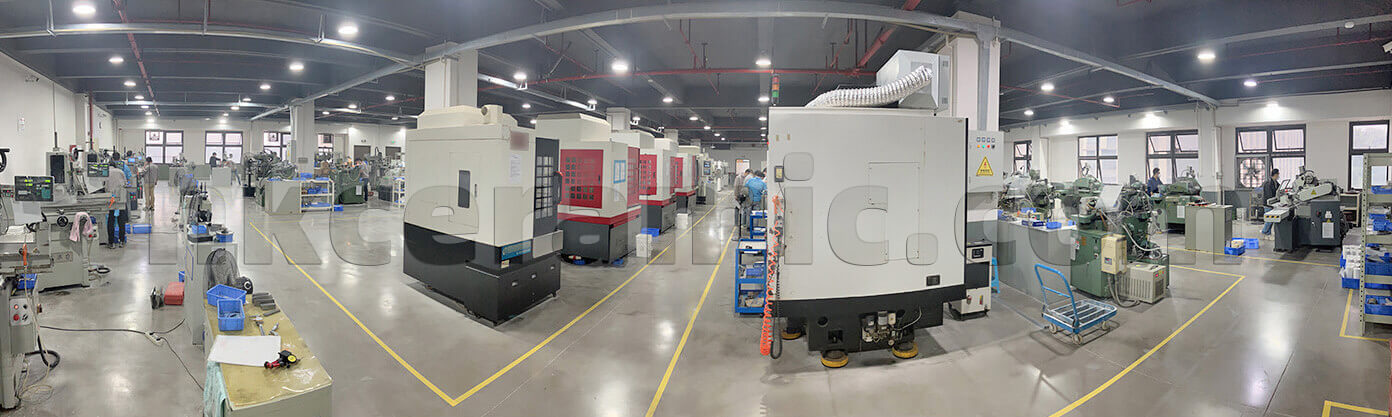
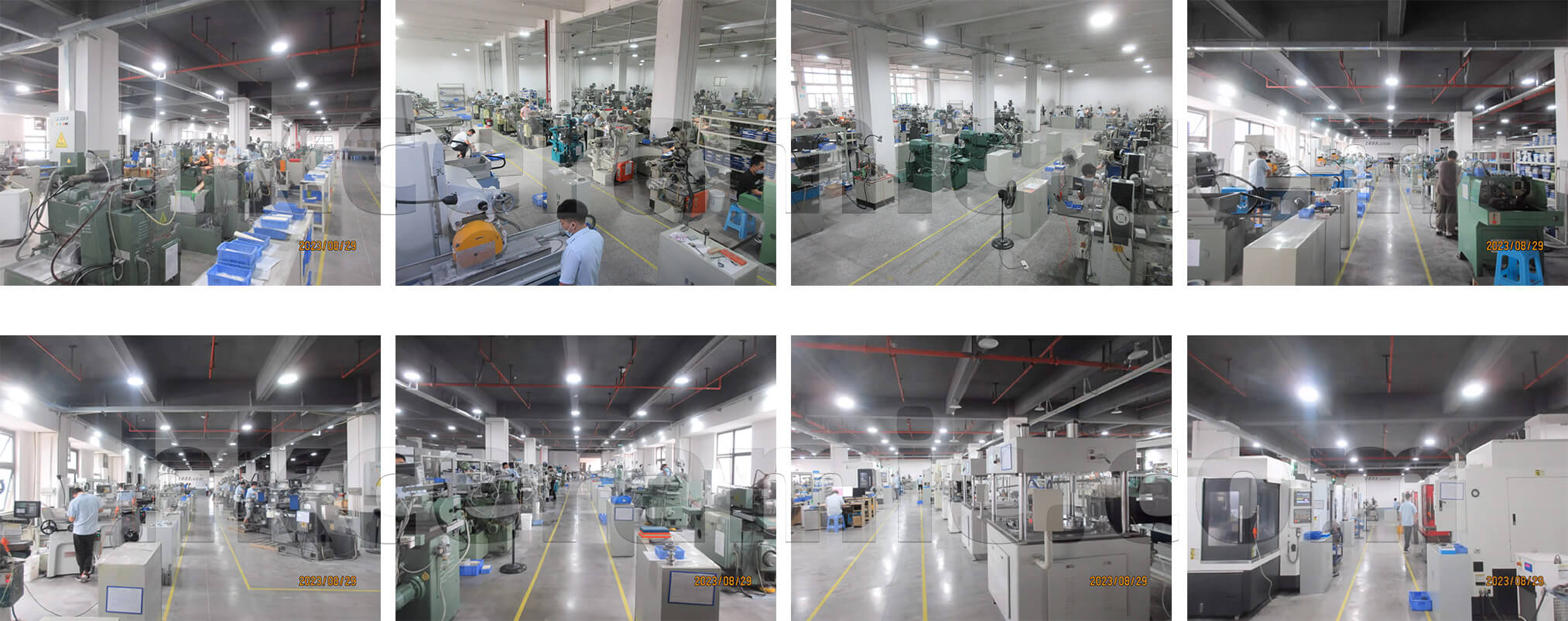
Comparison of ceramic material properties
Use our interactive ceramic material comparison chart to compare ceramic materials across different material properties.
Click the Property Button above to view the corresponding property comparison of precision ceramic materials
*The values in the table are typical material properties
Precision ceramic product customization process
Step 1
Contact us
Step 2
Technology Assessment
Step 3
Confirm the quotation
Step 4
Signing the contract
Step 5
Inspection and delivery
Step 6
Confirm Receipt