Silicon Nitride Ceramic Plunger
E-mail:sales01@hkceramic.com
Silicon nitride ceramic plunger, also known as an insulating ceramic piston, demonstrates the outstanding performance of silicon nitride ceramics as industrial-grade fasteners:
Excellent Mechanical Strength and Wear Resistance
With a high elastic modulus of 290 GPa and Vickers hardness reaching 1500 HV, these properties provide exceptional wear resistance and compressive strength, ensuring stability and long-term durability under high-load conditions.
High Heat Resistance and Thermal Shock Resistance
Capable of operating at temperatures up to 1200°C with a high coefficient of thermal shock stability up to 500°C, the plunger maintains dimensional stability and performance in environments with significant temperature fluctuations.
Superior Chemical Stability
The chemical inertness of silicon nitride allows it to perform well in various corrosive environments, making it particularly suitable for applications in chemical processing and medical equipment.
Excellent Sealing Performance and Low Friction
The smooth outer surface and precise machining dimensions of the plunger contribute to excellent sealing performance, reducing friction and wear during operation, thereby enhancing overall system efficiency.
Silicon nitride ceramic plungers find extensive applications in several demanding industrial settings, including:
Chemical Processing Equipment
Used in pumps and valves handling corrosive chemicals, the plunger's chemical stability and heat resistance ensure equipment reliability and safety.
Medical Devices
Utilized in medical equipment subjected to high-temperature and chemical sterilization processes to ensure safe and accurate operation.
Food Processing
Employed in equipment within the food industry where non-toxicity and corrosion resistance of silicon nitride plungers ensure food safety and processing efficiency.
High-Performance Pumps and Valves
Critical in industrial pumps and valves requiring superior sealing and durability, where the plunger's high temperature resistance and mechanical strength play a crucial role.
Silicon nitride ceramic plungers, with their outstanding wear resistance, high temperature performance, chemical stability, and excellent insulation properties, have become indispensable components in various extreme environments. These qualities make them particularly important in applications requiring high temperatures, high pressures, advanced cleanliness standards, and precise control, such as chemical processing, medical equipment, and food processing industries. The high performance and reliability of silicon nitride plungers make them superior alternatives to traditional metal pistons, meeting the modern industrial demand for high-tech materials.
In the field of precision ceramic processing and customization, our company specializes in producing various high-performance ceramic components, including zirconia ceramics, silicon nitride, aluminum nitride, and other products. These ceramic components possess excellent thermal stability, electrical insulation, high-temperature resistance, and wear resistance, widely applied in critical fields such as aerospace, electronics, machinery, defense, and automotive industries. Our products provide customers with crucial support and assurance, enhancing production efficiency and optimizing product performance.
Dongguan Haikun New Material Co., Ltd.
A global advanced precision ceramics (special ceramics) manufacturer, focusing on the development, design, production and sales of advanced precision ceramic products, covering zirconium oxide, aluminum oxide, silicon nitride and other materials, which are widely used in aviation, aerospace, military industry, medical and other fields
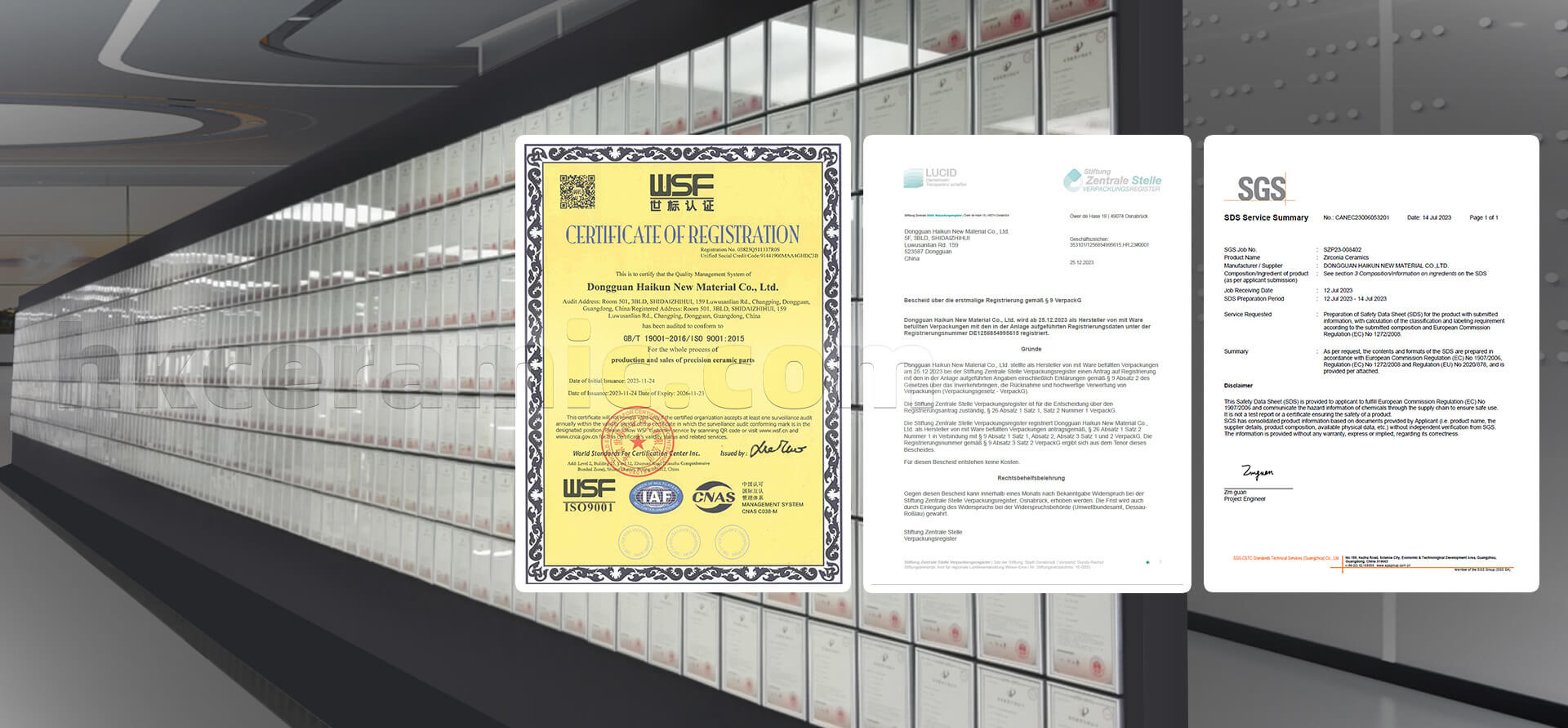
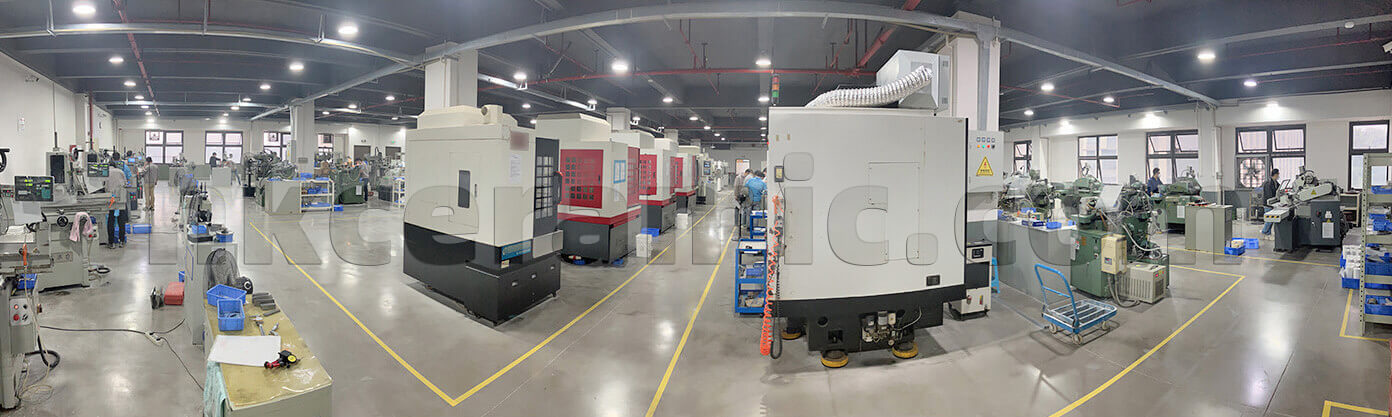
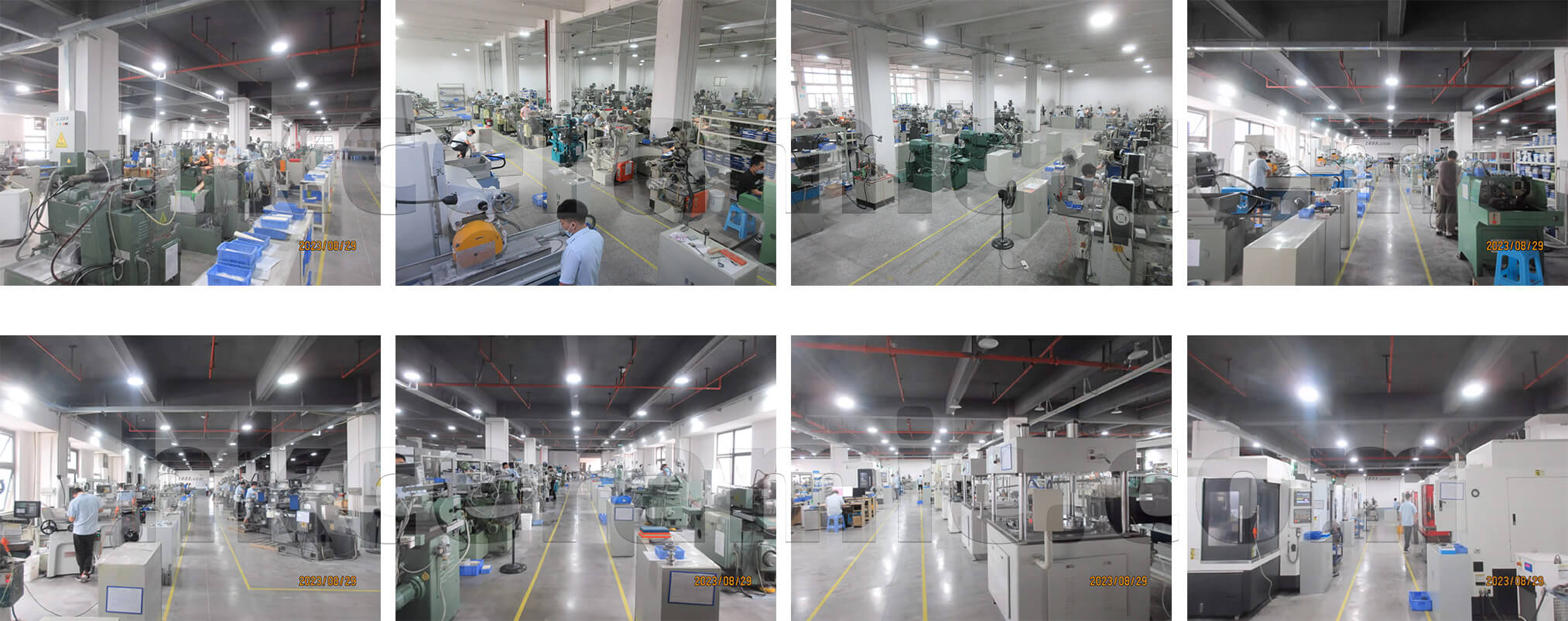
Comparison of ceramic material properties
Use our interactive ceramic material comparison chart to compare ceramic materials across different material properties.
Click the Property Button above to view the corresponding property comparison of precision ceramic materials
*The values in the table are typical material properties
Precision ceramic product customization process
Step 1
Contact us
Step 2
Technology Assessment
Step 3
Confirm the quotation
Step 4
Signing the contract
Step 5
Inspection and delivery
Step 6
Confirm Receipt