Silicon nitride ceramic welding rollers
E-mail:sales01@hkceramic.com
Silicon nitride ceramic welding rollers, also known as aluminum tube welding ceramic rollers, harness the unique properties of silicon nitride material to meet the demands of high-temperature welding processes:
High Wear Resistance and Heat Resistance
Silicon nitride boasts a Vickers hardness up to 1500 HV and can withstand temperatures up to 1200°C, making welding rollers excel under continuous high-temperature conditions, ideal for metal processing applications, especially aluminum tube welding.
Excellent Mechanical Strength
With an elastic modulus of 290 GPa and flexural strength of 600 MPa, silicon nitride ensures stability and durability of welding rollers under high pressure.
Thermal Shock Resistance and Low Thermal Expansion Coefficient
It exhibits a thermal shock stability coefficient at 500°C and a thermal expansion coefficient of 3.1×10-6/°C, ensuring dimensional stability and consistent performance of rollers in environments with significant temperature fluctuations.
Smooth Surface Treatment
The surface of welding rollers is exceptionally smooth, reducing surface damage to metal sheets or pipes during welding and enhancing operational efficiency.
Silicon nitride ceramic welding rollers play crucial roles in multiple key industrial sectors:
Metal Processing Industry
Especially in applications like aluminum tube welding, these welding rollers are used for conveying and supporting pipes or metal sheets, needing to withstand continuous high pressure and high temperatures.
Aerospace and Automotive Manufacturing
In the aerospace and automotive industries, these welding rollers are used for manufacturing parts and components that require high precision and durability.
Electronics
In the electronics sector, particularly in the manufacturing of components operating at high temperatures, silicon nitride welding rollers provide necessary heat resistance and stability.
Industrial Machinery and Equipment
In high-load and high-temperature industrial applications such as heavy machinery and production lines, welding rollers help improve productivity and reduce maintenance costs.
Silicon nitride ceramic welding rollers deliver outstanding performance in high-temperature and high-load industrial applications, thanks to their excellent heat resistance, mechanical strength, and wear resistance. These rollers not only enhance welding quality and efficiency but also reduce maintenance needs and operational costs, ensuring long-term stable operation. Their design and material optimization make silicon nitride welding rollers an ideal choice for metal processing and other demanding applications, particularly in advanced manufacturing fields that prioritize high performance and reliability.
In the realm of custom precision ceramic processing, our company specializes in producing various high-performance ceramic components, including zirconia ceramics, silicon nitride, aluminum nitride, and more. These ceramic components offer exceptional thermal stability, electrical insulation, high-temperature stability, and wear resistance, widely applied in critical fields such as aerospace, electronics, machinery, defense, and automotive. Our products provide crucial support and assurance to customers with their outstanding performance and reliability, contributing to enhanced production efficiency and optimized product performance.
Dongguan Haikun New Material Co., Ltd.
A global advanced precision ceramics (special ceramics) manufacturer, focusing on the development, design, production and sales of advanced precision ceramic products, covering zirconium oxide, aluminum oxide, silicon nitride and other materials, which are widely used in aviation, aerospace, military industry, medical and other fields
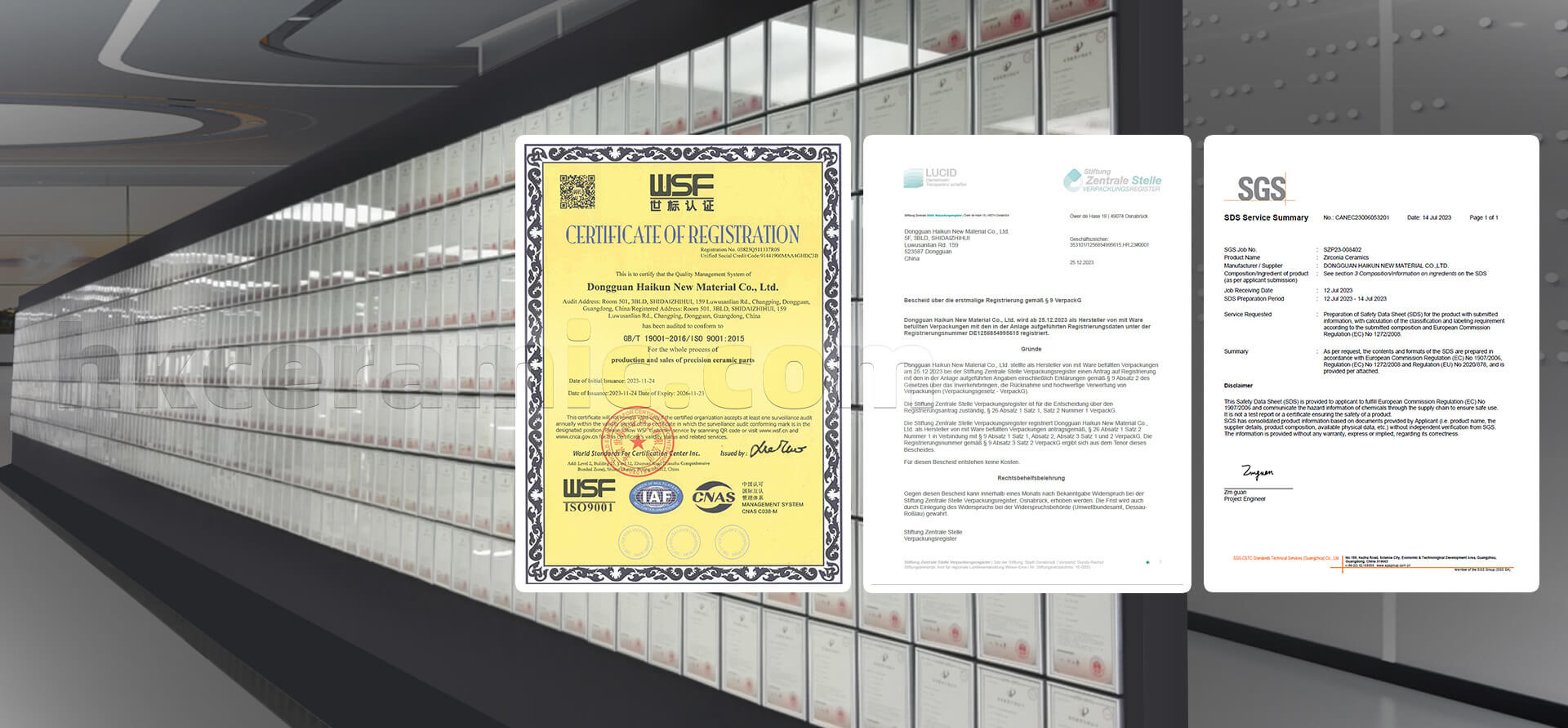
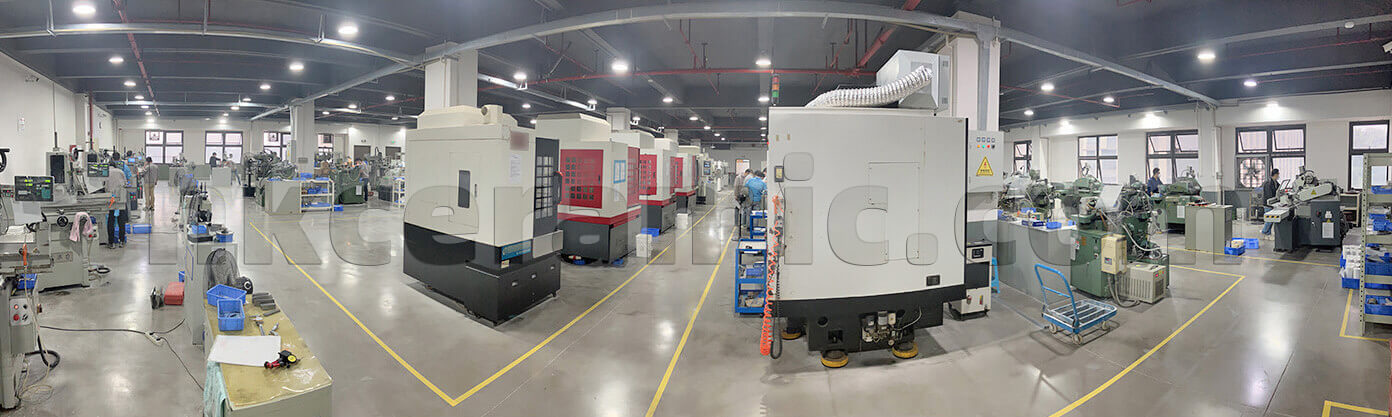
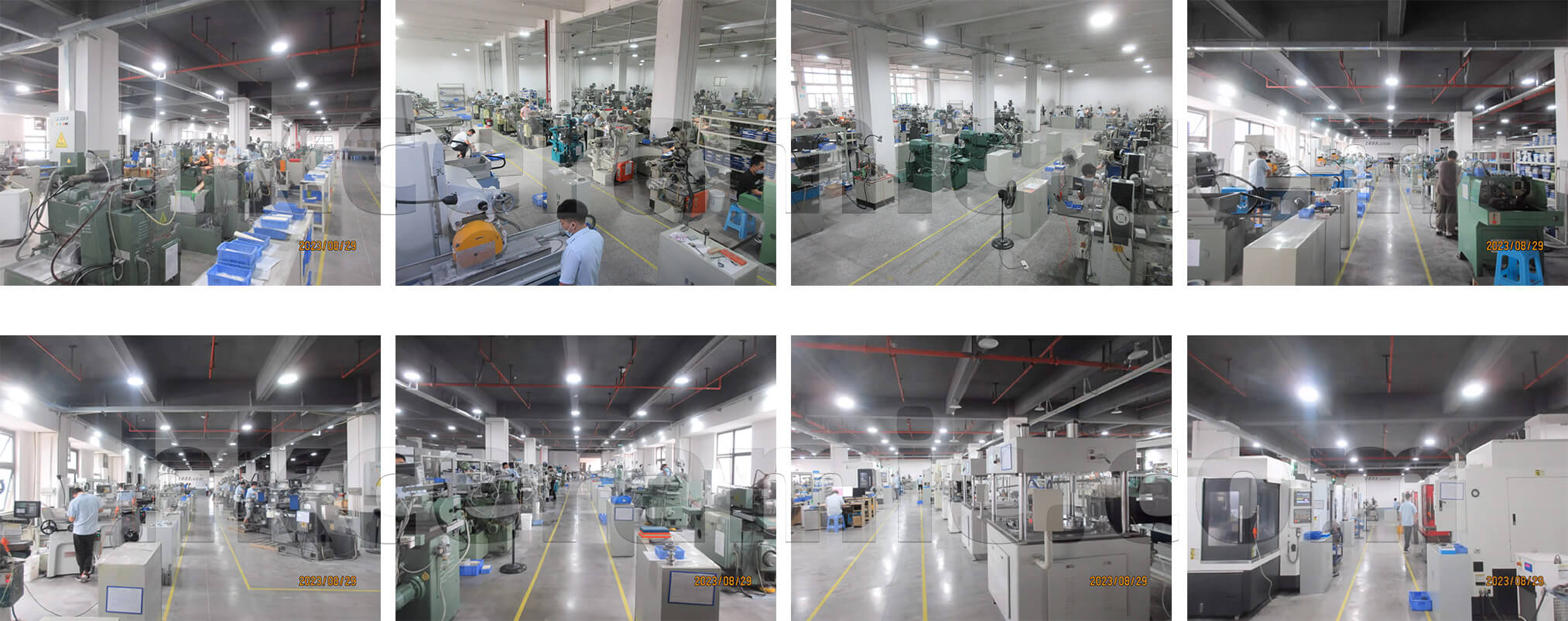
Comparison of ceramic material properties
Use our interactive ceramic material comparison chart to compare ceramic materials across different material properties.
Click the Property Button above to view the corresponding property comparison of precision ceramic materials
*The values in the table are typical material properties
Precision ceramic product customization process
Step 1
Contact us
Step 2
Technology Assessment
Step 3
Confirm the quotation
Step 4
Signing the contract
Step 5
Inspection and delivery
Step 6
Confirm Receipt