Covered zirconia ceramic crucible
E-mail:sales01@hkceramic.com
Covered zirconia ceramic crucibles, also known as corrosion-resistant high-temperature ceramic grinding jars, feature multiple carefully designed characteristics to suit rigorous industrial and laboratory environments:
Structure and Design
The crucible design features a smooth exterior shell and a tightly fitting lid. This design effectively prevents sample contamination and loss of volatile substances during heating, while also enhancing thermal efficiency to maintain a constant temperature inside the crucible.
Thermal Efficiency and Safety
The presence of the lid not only improves thermal efficiency for more uniform temperatures but also protects operators from direct exposure to high temperatures, ensuring safety in experiments and production.
Material Advantages
Zirconia ceramic has a thermal expansion coefficient of 9.6×10-6℃ and excellent thermal shock resistance up to 250℃, making the crucible capable of withstanding drastic temperature changes. It is highly suitable for applications requiring frequent heating and cooling.
Chemical Stability and Durability
Zirconia ceramic exhibits exceptional chemical stability and a 0% water absorption rate, ensuring corrosion resistance and long-term durability when handling strong acids, alkalis, or other corrosive substances.
Covered zirconia ceramic crucibles excel in multiple high-demand application fields, particularly in environments requiring high temperatures, high purity, and chemical stability:
High-Temperature Chemical Reactions
Due to their high temperature resistance and chemical stability, these crucibles are highly suitable for various high-temperature chemical reactions, capable of enduring continuous thermal cycles without performance degradation.
Metal and Ore Melting
The crucibles' heat resistance and resistance to chemical corrosion make them an ideal choice for melting metals and ores, particularly in refining high-purity metals.
Scientific Research and Material Analysis
In scientific research and material analysis, where precise temperature control and prevention of sample contamination are crucial, covered zirconia ceramic crucibles provide these necessary conditions.
Covered zirconia ceramic crucibles offer reliable solutions in demanding experimental and industrial environments with their outstanding design and material performance. Their structural design optimizes thermal efficiency and chemical stability, ensuring efficient and safe operations under extreme conditions. These crucibles are indispensable tools in high-temperature, high-purity experiments and production activities, demonstrating the high performance and adaptability of zirconia ceramic materials.
In the field of customized precision ceramic processing, our company specializes in producing various high-performance ceramic components, including zirconia ceramics, silicon nitride ceramics, aluminum nitride ceramics, and more. These ceramic components exhibit excellent thermal stability, electrical insulation, high temperature resistance, and wear resistance, widely applied in critical sectors such as aerospace, electronics, machinery, defense, and automotive industries. Our products provide crucial support and assurance to customers, helping them enhance production efficiency and optimize product performance.
Dongguan Haikun New Material Co., Ltd.
A global advanced precision ceramics (special ceramics) manufacturer, focusing on the development, design, production and sales of advanced precision ceramic products, covering zirconium oxide, aluminum oxide, silicon nitride and other materials, which are widely used in aviation, aerospace, military industry, medical and other fields
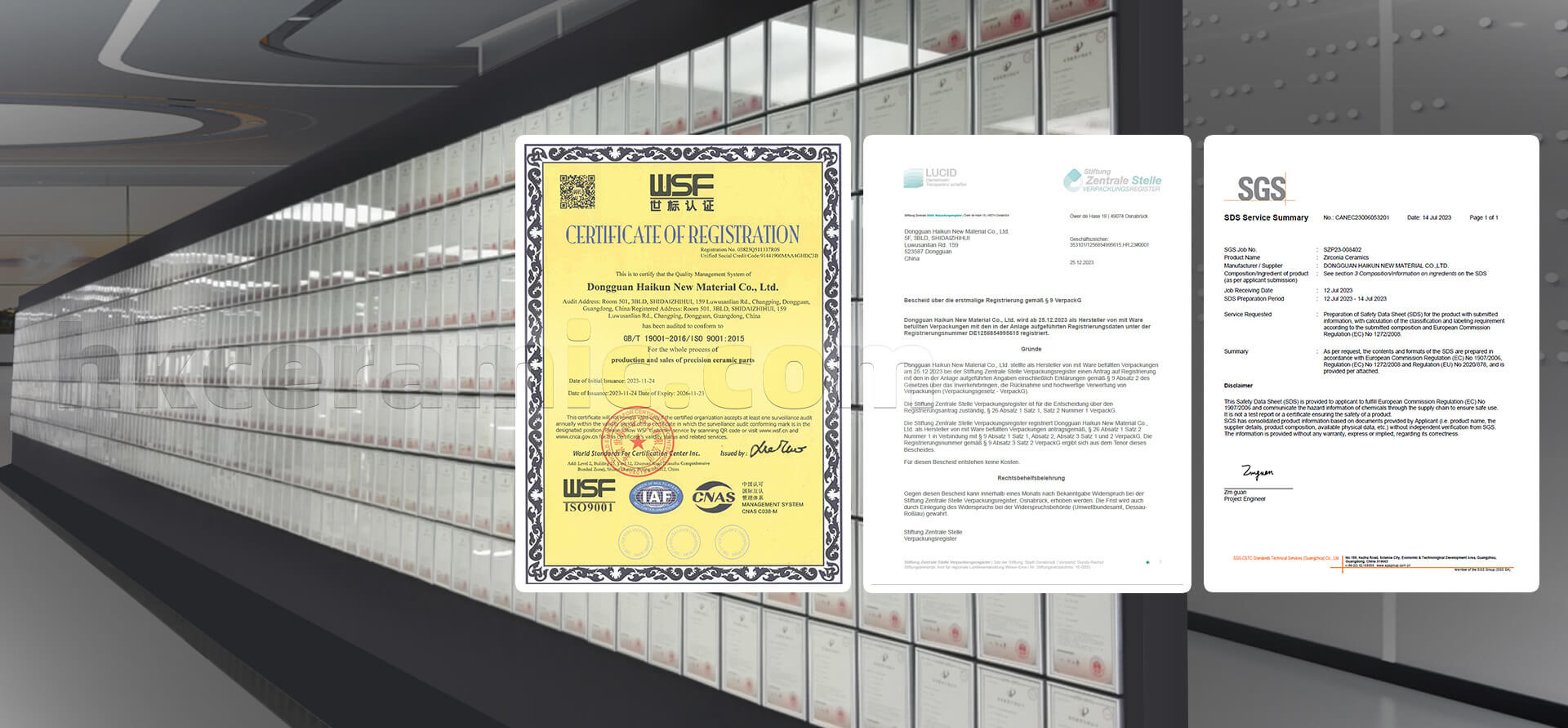
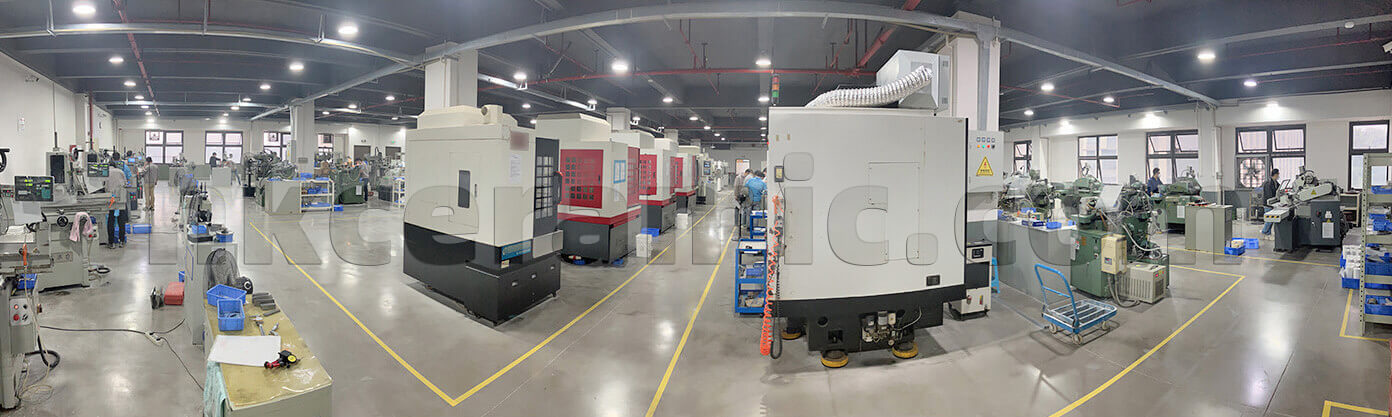
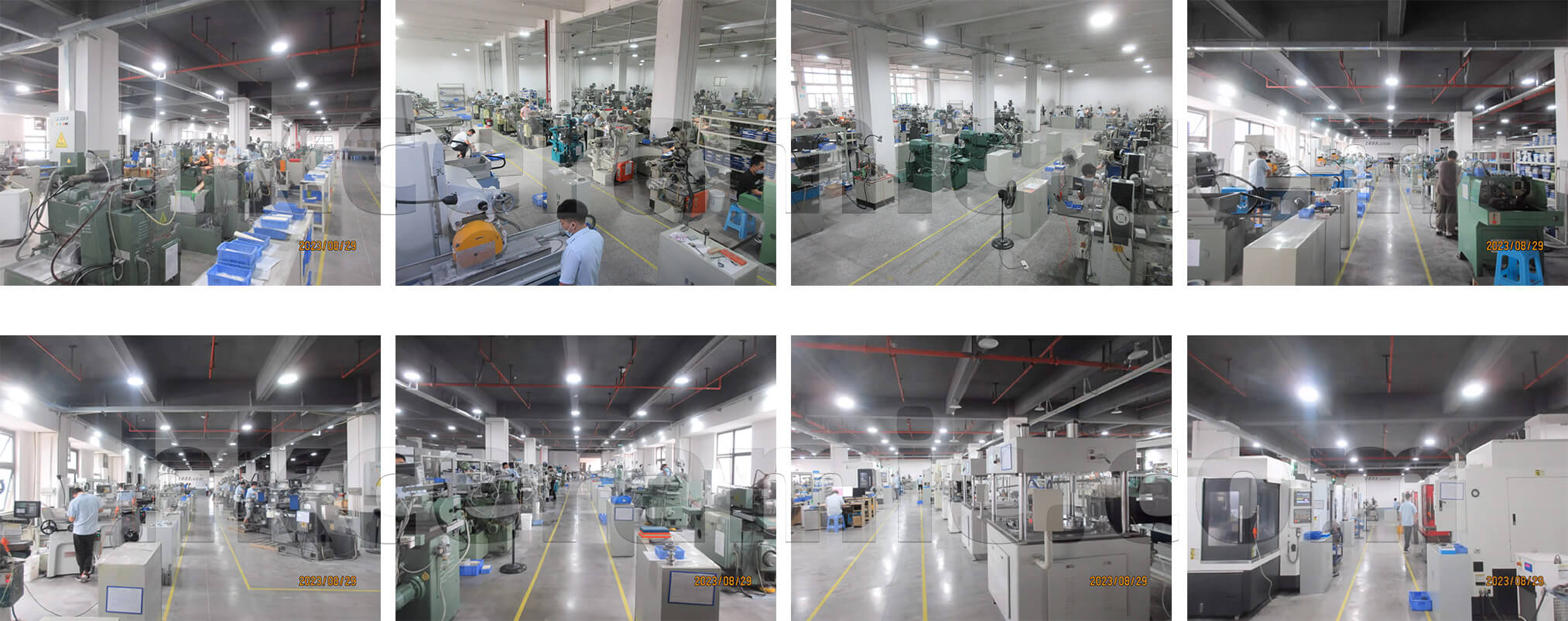
Comparison of ceramic material properties
Use our interactive ceramic material comparison chart to compare ceramic materials across different material properties.
Click the Property Button above to view the corresponding property comparison of precision ceramic materials
*The values in the table are typical material properties
Precision ceramic product customization process
Step 1
Contact us
Step 2
Technology Assessment
Step 3
Confirm the quotation
Step 4
Signing the contract
Step 5
Inspection and delivery
Step 6
Confirm Receipt