Large-sized zirconia ceramic rollers
E-mail:sales01@hkceramic.com
The design of large-sized zirconia ceramic rollers features several prominent characteristics, optimizing their performance in industrial processing:
Material Composition
The rollers are made from high-purity zirconia ceramic with a content of 94.40% zirconia, ensuring robustness and durability. Additionally, zirconia ceramic boasts a Vickers hardness of up to 1175 GPa, providing exceptional wear resistance and corrosion resistance, making it highly suitable for demanding industrial environments.
Surface Design
The roller surface features a unique raised texture that enhances material grip and improves transmission efficiency. Precise texture machining ensures uniformity and accuracy during processing of metal sheets or other hard materials, crucial for maintaining product quality and consistency.
Wear Resistance and Durability
The rollers have a bending strength of up to 800 MPa and compressive strength of 2000 MPa, enabling them to withstand the challenges of heavy-duty operations on high-load production lines. The highly smoothed surface treatment also reduces friction and wear, enhancing overall performance and longevity.
Appearance and Quality Standards
The rollers are meticulously smoothed on their outer surfaces to minimize friction and wear, thereby enhancing their performance on the production line. The white surface also reflects the purity of zirconia material and high-quality standards. These rollers are suitable for various manufacturing environments, capable of enduring heavy-duty operations and providing long-term reliability.
Zirconia ceramic rollers are suitable for various manufacturing environments, especially those handling high-hardness materials or operating in high-temperature settings. Due to zirconia ceramic's exceptional wear resistance, mechanical strength, thermal shock resistance, and corrosion resistance, these rollers are particularly well-suited for industries involved in metal processing, plastic processing, and other industrial materials. Their durability and reliability shine in heavy-duty work environments like continuous production lines and high-load processing equipment.
Large-sized zirconia ceramic rollers deliver outstanding industrial processing performance through their excellent material properties and innovative design. Their high hardness, excellent wear resistance, compressive strength, and unique surface texture design ensure high efficiency and long-term stability in demanding industrial environments. These features make zirconia ceramic rollers an ideal choice for heavy-duty operations, enhancing machining precision, production efficiency, and maintaining high standards of product quality and consistency.
In the field of customized precision ceramic processing, our company specializes in producing various high-performance ceramic components, including zirconia ceramics, silicon nitride ceramics, aluminum nitride ceramics, and more. These ceramic components offer excellent thermal stability, electrical insulation, high-temperature resistance, and wear resistance, widely used in critical sectors such as aerospace, electronics, machinery, defense, and automotive industries. Our products provide crucial support and assurance to customers, helping them enhance production efficiency and optimize product performance.
Dongguan Haikun New Material Co., Ltd.
A global advanced precision ceramics (special ceramics) manufacturer, focusing on the development, design, production and sales of advanced precision ceramic products, covering zirconium oxide, aluminum oxide, silicon nitride and other materials, which are widely used in aviation, aerospace, military industry, medical and other fields
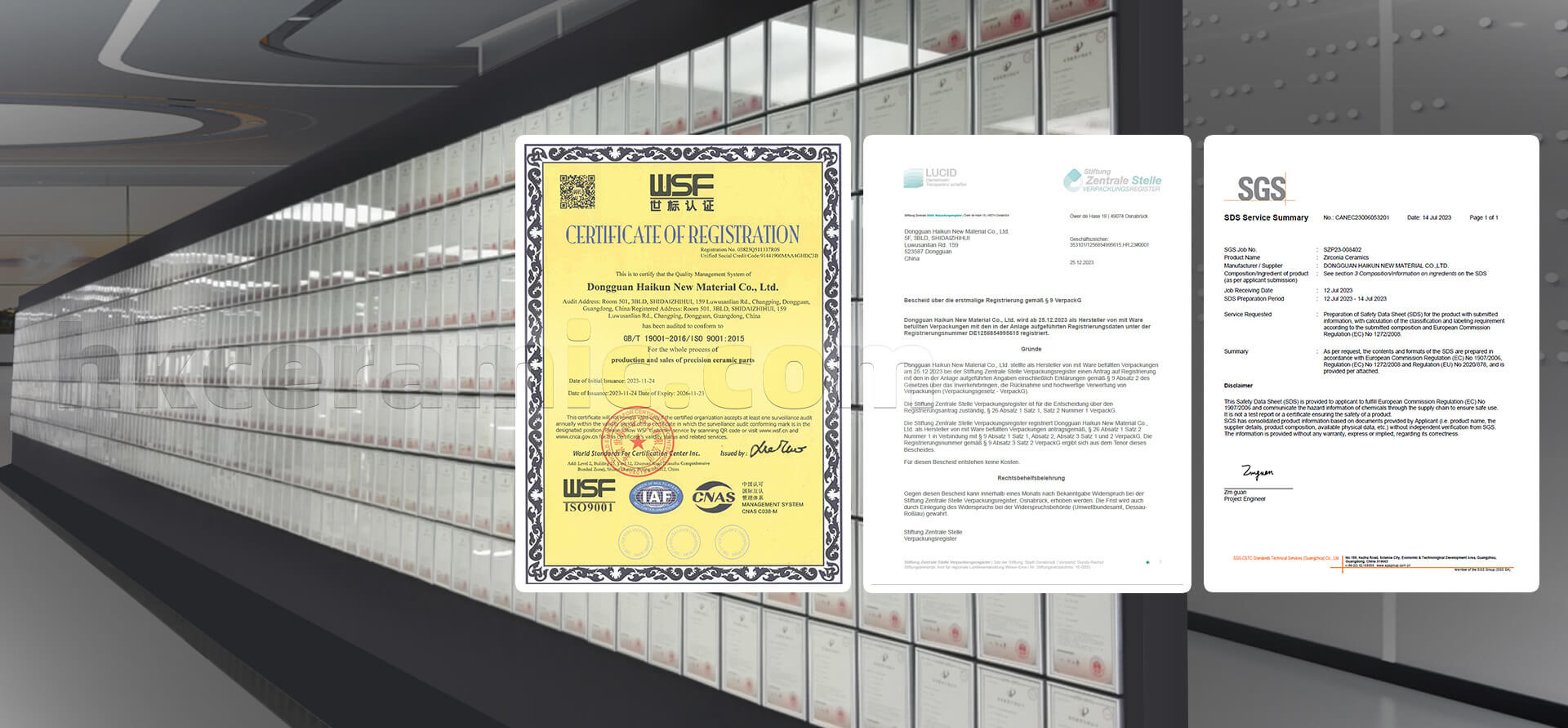
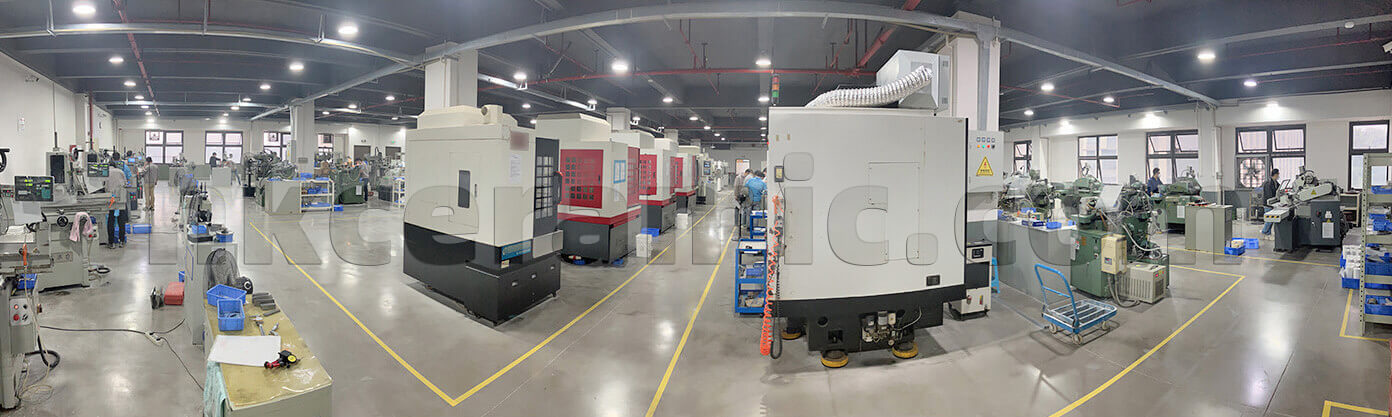
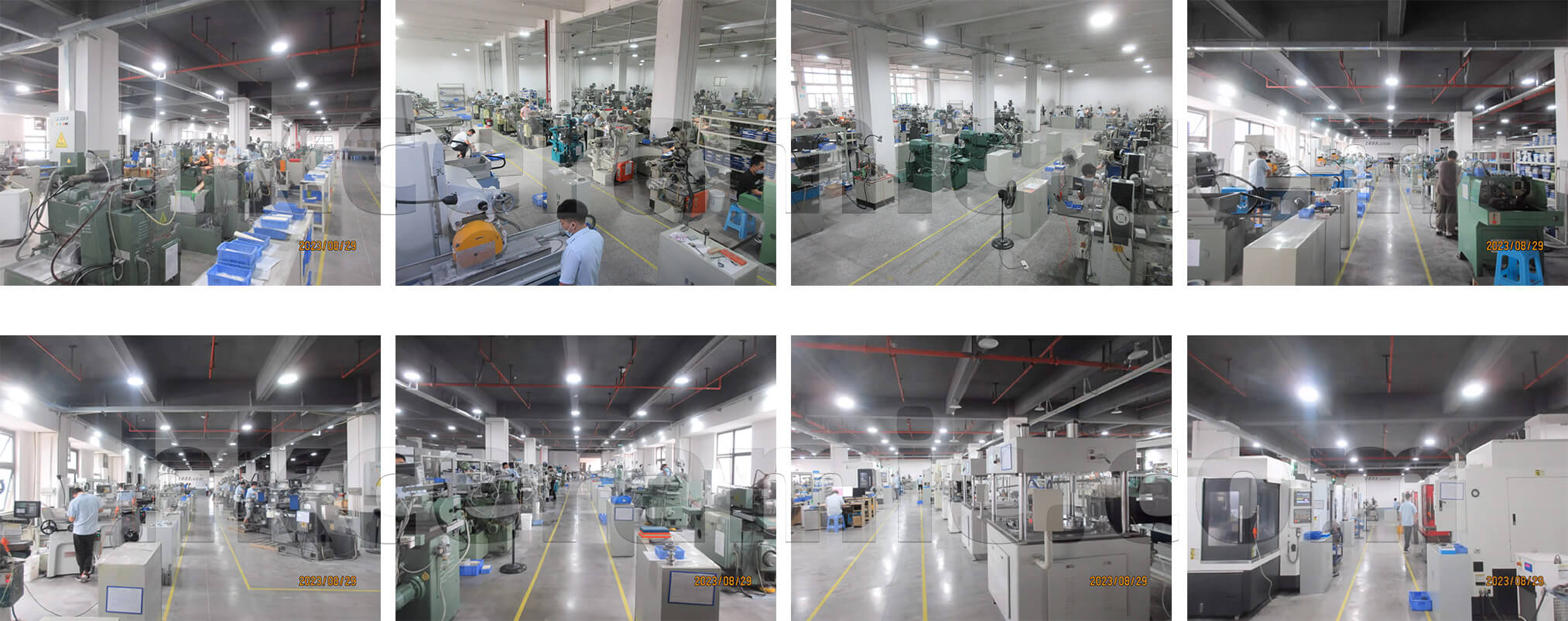
Comparison of ceramic material properties
Use our interactive ceramic material comparison chart to compare ceramic materials across different material properties.
Click the Property Button above to view the corresponding property comparison of precision ceramic materials
*The values in the table are typical material properties
Precision ceramic product customization process
Step 1
Contact us
Step 2
Technology Assessment
Step 3
Confirm the quotation
Step 4
Signing the contract
Step 5
Inspection and delivery
Step 6
Confirm Receipt